RPI’s 20 Stories for 20 Years – Mini-Tractor Collaboration
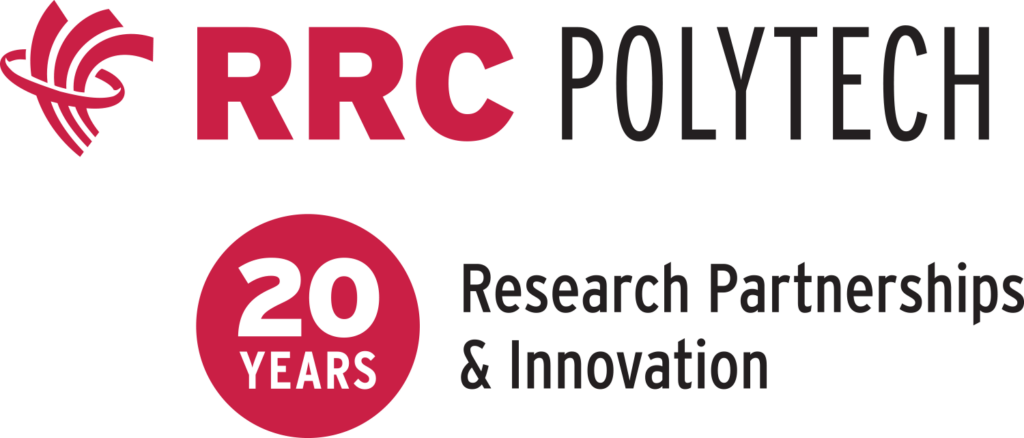
To demonstrate the impact that applied research projects make on all Manitobans, we present RPI’s 20 Stories for 20 Years. A compilation showcasing successful partnerships from the past and the present, with a constant focus on the future.
Driven by the need for an agricultural safety training tool, a collaboration between RRC Polytech, the University of Manitoba and Keystone Agricultural Producers (KAP) produced a unique vehicle to help predict, teach and demonstrate tractor roll overs.
The Mini Roll Over Training Tractor (Mini ROTT) was publicly demonstrated at the UM’s Glenlea Research Station in the summer of 2020. Approximately the size of an average lawn tractor but with the appearance of a traditional tractor, the radio-controlled Mini ROTT will be used for teaching and demonstration of roll overs and activities that will enhance students’ and farmers’ understanding of farm safety practices.
“Keystone Agricultural Producers is proud to be a part of the roll over training tractor (ROTT) project through our Manitoba Farm Safety Program. This innovative tool will promote the need for safety awareness and training across our sector to reduce the risk of serious injury in the operation of tractors and large equipment on farms across the province,” said the late and legendary Bill Campbell, then President, KAP.
“The partnership we have forged with the University of Manitoba and Red River College (Polytechnic) shows the importance of our industry to this province and showcases some of the brightest minds and ingenuity we have here in Manitoba.”
The project was initiated by the UM’s Faculty of Agricultural and Food Sciences to supplement hands-on safety workshops developed for diploma students and farmers. The UM teamed up with KAP’s Manitoba Farm Safety Program (now known as FarmSafe Manitoba) staff to explore the concept of a remote-controlled tractor as an interactive training tool for teaching roll over prevention strategies.
UM and KAP then engaged with RRC Polytech’s Technology Access Centre for Aerospace & Manufacturing (TACAM) and Vehicle Technology & Energy Centre (VTEC) to complete the fabrication process. The research staff at TACAM designed and built the tractor, with support from the VTEC team on the electronics and systems control components.
“Working with Keystone Agricultural Producers and the University of Manitoba on the roll over training tractor (ROTT) is the perfect demonstration of the value of applied research: providing tangible solutions to real-world problems,” said Fred Meier, President & CEO, RRC Polytech.
“The ROTT highlights the skill and expertise of our TACAM and VTEC teams. We’re proud to play a role in farm safety awareness and supporting the agriculture industry in Manitoba.”
Funding for the project came from a variety of sources, including the Faculty of Agricultural and Food Sciences Endowment Fund, the Natural Sciences and Engineering Research Council of Canada through RRC Polytech’s TACAM and VTEC-Innovation Enhancement grants, and Keystone Agricultural Producers.
RRC Polytech, FarmSafe Manitoba and UM staff continue to collaborate on expanded tractor training and developing programs aimed at creating a safer agri-food industry. In fact, the Mini ROTT is currently back in the Smart Factory at NDC as the TACAM team makes some necessary upgrades. It will then return to the Glenlea Research Station where it can be utilized for farm safety training for post-secondary students and Manitoba farmers.
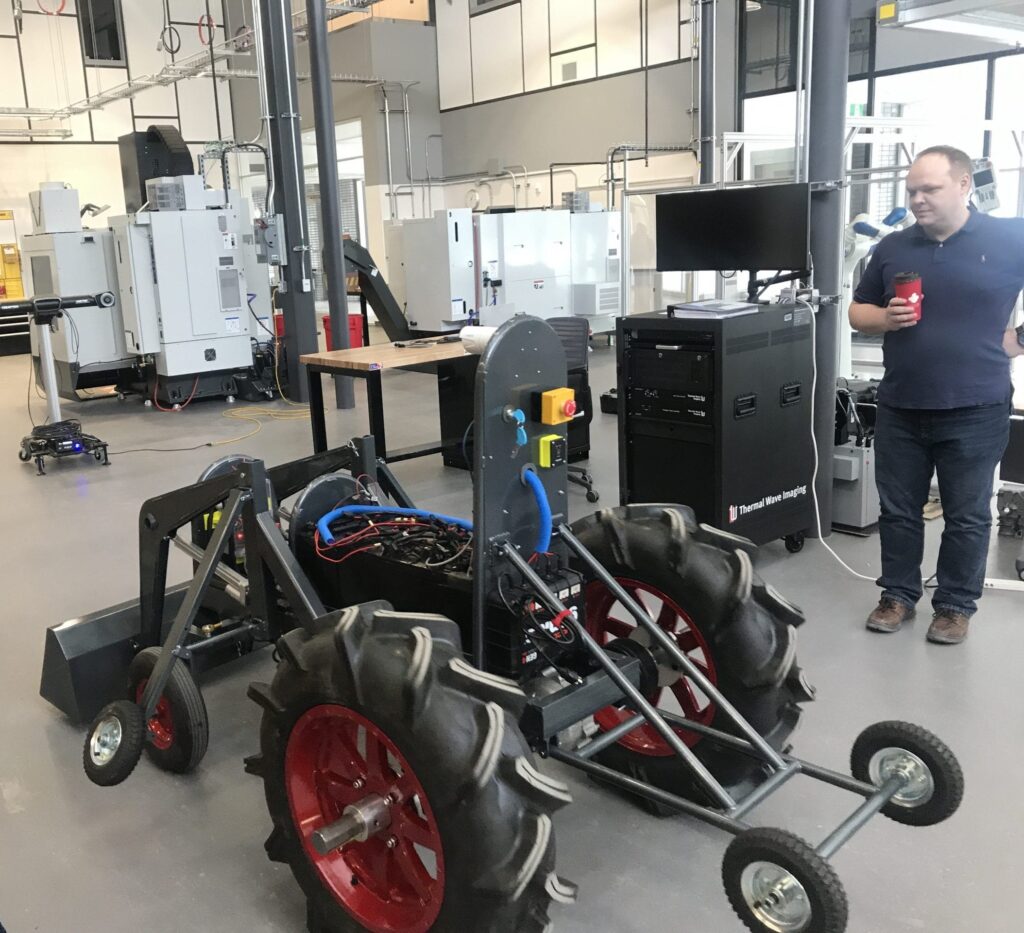